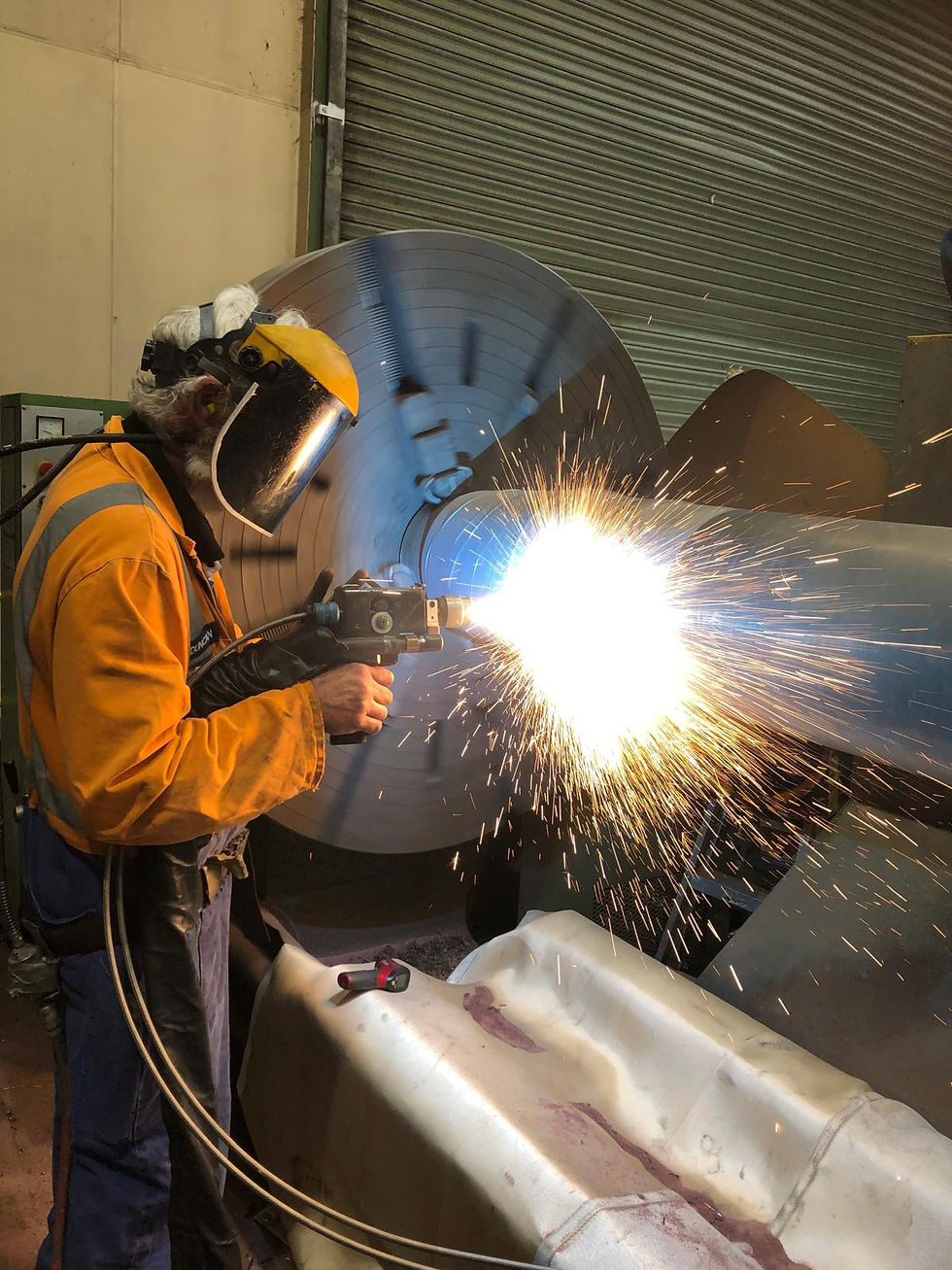
Machining
Machining Services: Precision, Versatility, and Quality
At Triple R Engineering, we provide comprehensive machining services with the flexibility to handle projects of all sizes and complexities. Our facilities and skilled operators ensure precision and efficiency for every job, whether it involves heavy CNC machinery or general machine tools.
Why Choose Triple R Engineering for Machining?
-
Advanced Equipment: From heavy-duty CNC machinery to versatile general tools, we’re equipped to tackle diverse machining requirements.
-
Dedicated Workshop: Our 365sqm covered machining workshop is designed for efficiency and productivity, accommodating a wide range of projects.
-
Experienced Operators: Our skilled team is committed to delivering top-quality results on every project.
Our Machining Capabilities
We offer a full suite of machining services to meet your specific needs, including:
-
Turning: Precision shaping of rotational components.
-
Milling: Accurate cutting and shaping for custom parts.
-
CNC Milling: High-precision automated solutions for complex geometries.
-
Universal Grinding: Versatile grinding for smooth, uniform finishes.
-
Surface Grinding: Perfect flatness and surface quality.
-
Superfining: Exceptional finishing for high-performance applications.
Whether you need custom parts, component restoration, or precision machining, Triple R Engineering is equipped to deliver reliable, high-quality results tailored to your requirements.
Contact us today to discuss your machining needs and experience our exceptional service.


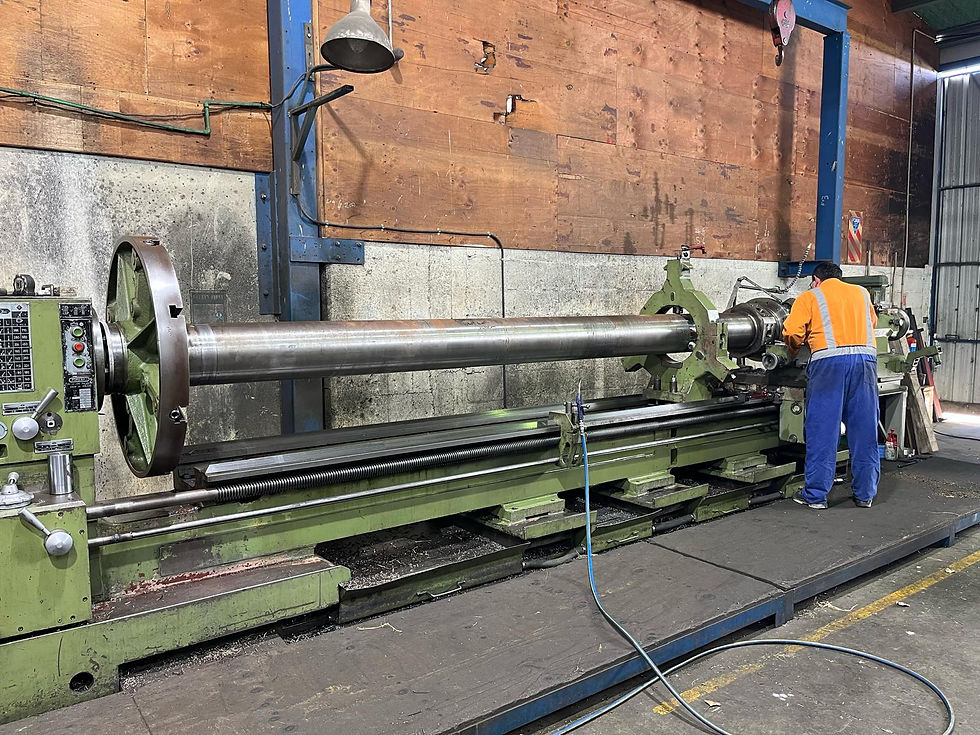
Industrial Metal Spraying
Industrial Metal Spraying Services: Restore, Protect, and Enhance Components
At Triple R Engineering, we specialise in metal spraying to refurbish worn components and protect new ones across major industries. With advanced technology and expertise, we extend the life of critical components subjected to wear and tear during operation, ensuring optimal performance and durability.
Why Choose Metal Spraying?
-
Refurbish Worn Components: Restore functionality to revolving parts with precision.
-
Protect New Components: Enhance durability with hardwearing metal and ceramic coatings.
-
Wide Material Selection: Tailored solutions to suit virtually any surface or application.
Our Metal Spraying Capabilities
We offer a comprehensive range of advanced coatings to meet diverse industry needs:
-
Arc Spray: Durable coatings for industrial applications.
-
Ceramic Coatings: High-resistance solutions for extreme conditions.
-
Tungsten Carbide Coatings: Exceptional wear and abrasion resistance.
-
Plasma Spraying: Advanced coatings for precision and performance.
-
High-Velocity Oxy-Fuel (HVOF): Robust protection for high-stress environments.
-
Engineering Repair & Anti-Corrosion Systems: Long-lasting solutions for structural integrity.
-
Non-Ferrous Metals: Zinc, aluminum, bronze, copper, white metal, and more.
-
Ferrous Metals: Including stainless steel alloys for heavy-duty applications.
Grit Abrasive Blasting: Precision Surface Preparation for Optimal Results
At Triple R Engineering, we provide professional grit abrasive blasting services in our fully dedicated on-site facility. Designed for efficiency and precision, our grit blasting capabilities ensure thorough surface preparation to achieve bare metal finishes, meeting the highest industry standards.
Why Choose Triple R Engineering for Grit Blasting?
-
SA3 Standards: Achieve perfectly clean surfaces for superior coating adhesion.
-
Versatile Abrasives: A variety of grit materials tailored to specific applications.
-
Material-Sensitive Techniques: Adjustable pressures to suit different materials and purposes.
-
Safety and Containment: Our factory blast booth ensures a safe, controlled environment.
-
Comprehensive Capability: From small components to large-scale items, we handle it all.
Applications of Grit Abrasive Blasting
-
Surface Preparation: Ideal for removing rust, old coatings, and contaminants.
-
Metal Cleaning: Restores surfaces to bare metal for repainting or re-coating.
-
Pre-Finishing: Prepares components for welding, coating, or other treatments.
-
Versatility: Suitable for a wide range of industries and materials.
Whether you’re looking to restore worn parts or enhance the lifespan of new components, our metal spraying services offer a cost-effective, efficient, and high-quality solution.
Contact Triple R Engineering today to discuss your project and discover how our metal spraying expertise can benefit your operations.


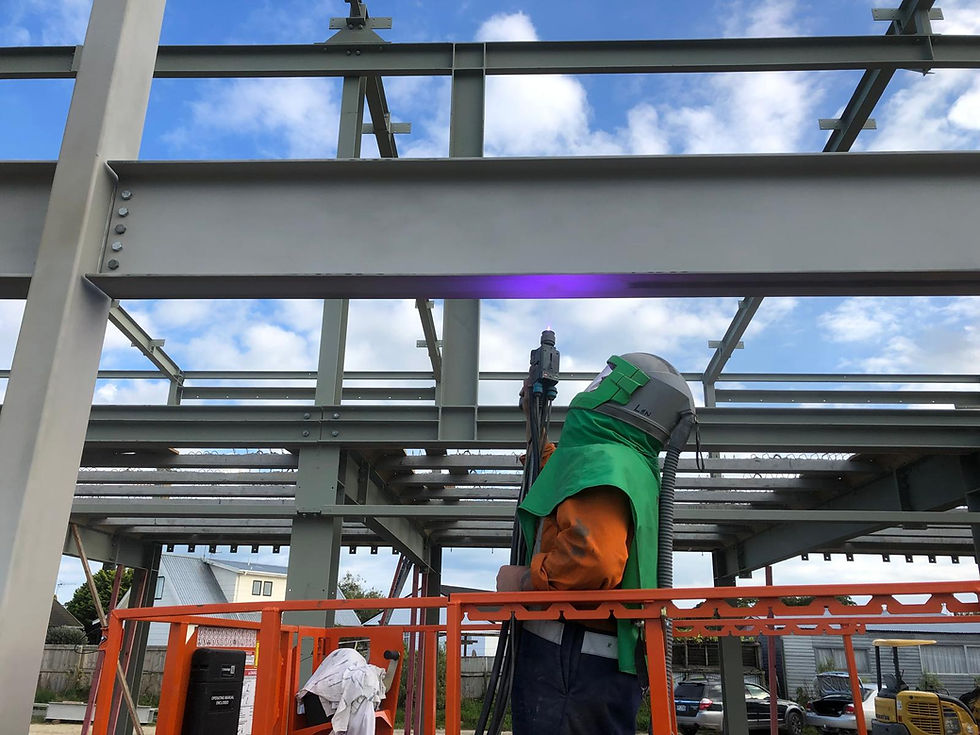
Welding
Expert Welding Services: Precision Repairs and Durable Builds
At Triple R Engineering, our skilled welders bring years of expertise and advanced techniques to every project. Specialising in a wide range of welding methods, we provide high-quality solutions tailored to restore, repair, and enhance your components with precision and durability.
Why Choose Triple R Engineering for Welding?
-
Extensive Knowledge: Decades of experience in welding and overlay techniques ensure reliable results.
-
Custom Solutions: Techniques and materials are chosen to suit each component’s application.
-
Quality Restoration: Broken or worn components are rebuilt to "as-new" condition with minimized distortion and stress.
Our Welding Capabilities
We offer a diverse range of welding services to meet various industrial needs, including:
-
Hard Face Build-Ups: Using specialized wires to extend component lifespan under high wear conditions.
-
Component Restoration: Best practices to rebuild worn parts with reduced stress and distortion.
-
Electrode Arc Welding: Reliable and efficient for various applications.
-
MIG Welding: Precision welding for stainless steel, aluminum, steel, and hard-facing projects.
-
TIG Welding: High-precision welding for stainless steel, aluminum, steel, cast iron, and hard-facing applications.
Whether you need to repair damaged components, restore worn parts, or build hard-wearing surfaces, Triple R Engineering delivers expert welding services to meet your exact requirements.
Contact us today to learn more about our welding solutions and how we can support your project.



Manufacturing & Fabrication
Manufacturing & Fabrication Services: Custom Solutions from Start to Finish
At Triple R Engineering, we specialize in manufacturing and fabricating a wide variety of products to meet your exact needs. From concept to completion, we collaborate closely with our customers to confirm or develop specifications and designs, ensuring every component is crafted with precision in our fully equipped, one-stop facility. This streamlined approach saves time and reduces costs.
Why Choose Triple R Engineering for Manufacturing & Fabrication?
-
End-to-End Solutions: From design consultation to final production, we handle every step in-house.
-
Customized Expertise: Tailored solutions to match your project’s specific requirements.
-
Cost Efficiency: A single-source facility for faster turnaround and reduced expenses.
Our Capabilities
We manufacture and fabricate a diverse range of products for industrial applications, including:
-
Conveyors: Engineered for reliable material handling.
-
Frames: Sturdy and precise fabrication for structural and industrial needs.
-
Flood Gates: Robust and durable for water control applications.
-
Straight-Bladed Fans: Designed for efficiency and performance.
-
Dewatering Screws: High-quality fabrication for fluid separation.
-
Shafts, Pins, Rams, and Axles: Precision-crafted components for heavy-duty performance.
Our team’s expertise and dedication to quality ensure that every product we manufacture or fabricate meets the highest industry standards.
Contact Triple R Engineering today to discuss your manufacturing and fabrication needs and see how our solutions can elevate your project.

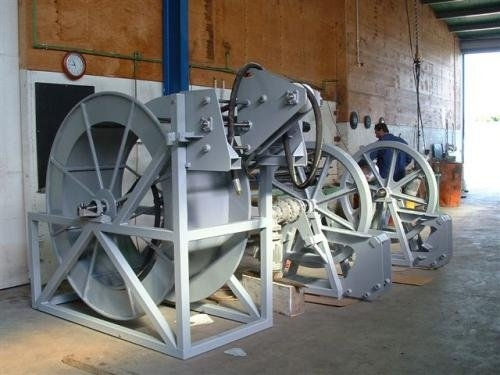

Zinc Arc Spraying
Zinc Arc Spraying: Versatile Anti-Corrosion Protection
At Triple R Engineering, we provide Zinc Arc Spraying as a reliable and flexible alternative to hot-dip galvanising. This innovative method is perfect for coating large or complex items that may not fit into traditional hot-dip baths, offering unmatched convenience and performance.
Why Choose Zinc Arc Spraying?
-
On-Site Application: Ideal for components that cannot be transported to a coating facility.
-
Cost-Effective: An affordable yet durable solution for corrosion protection.
-
Proven Performance: Delivers reliable results, even in harsh environments.
-
Marine-Grade Protection: Rated for use in C5 Marine classified areas in New Zealand.
-
Custom Finishes: Options to paint or seal for enhanced durability and aesthetics.
Applications of Zinc Arc Spraying
-
Structural Steel and Large Components: Protects oversized items with ease.
-
Marine and Coastal Equipment: Ensures long-term resistance to saltwater and humidity.
-
Industrial Machinery: Shields critical components from wear and corrosion.
-
Custom Coatings: Perfect for both standalone protection or as a base layer for painted finishes.
Zinc Arc Spraying provides a highly adaptable and effective solution for safeguarding your assets against corrosion.
Contact Triple R Engineering today to discuss your project and learn how our Zinc Arc Spraying services can protect your investments.
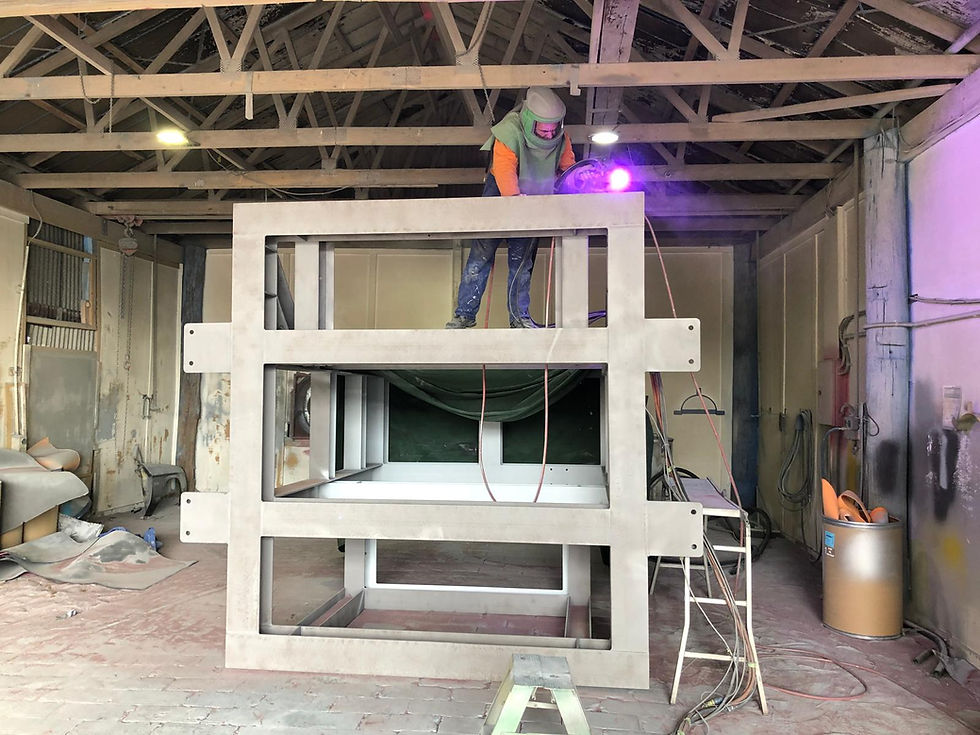

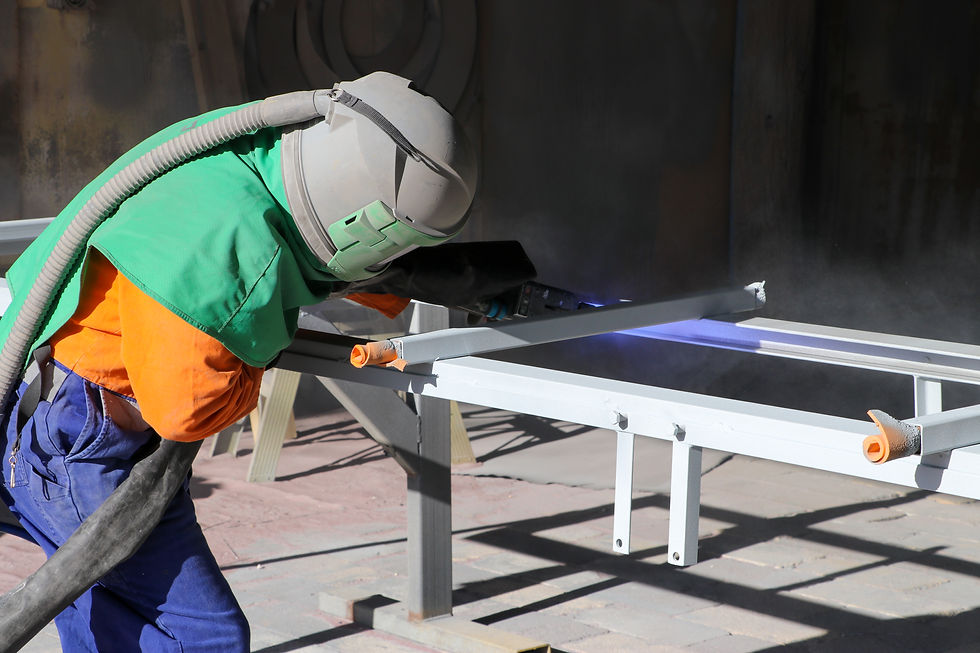
Painting
Industrial Spray Painting Services
Our team specialises in industrial spray painting, delivering durable, high-quality finishes tailored to heavy industry requirements.
-
Expert application of protective coatings enhances durability in harsh environments.
-
Precision spray painting of components like fuel tanks, structural frames, and heavy machinery parts.
-
Surface preparation techniques ensure optimal paint adhesion and longevity.
-
Colour coding and custom finishes are available to meet client specifications and industry standards.
-
Use of high-performance paints that offer corrosion resistance and wear protection.

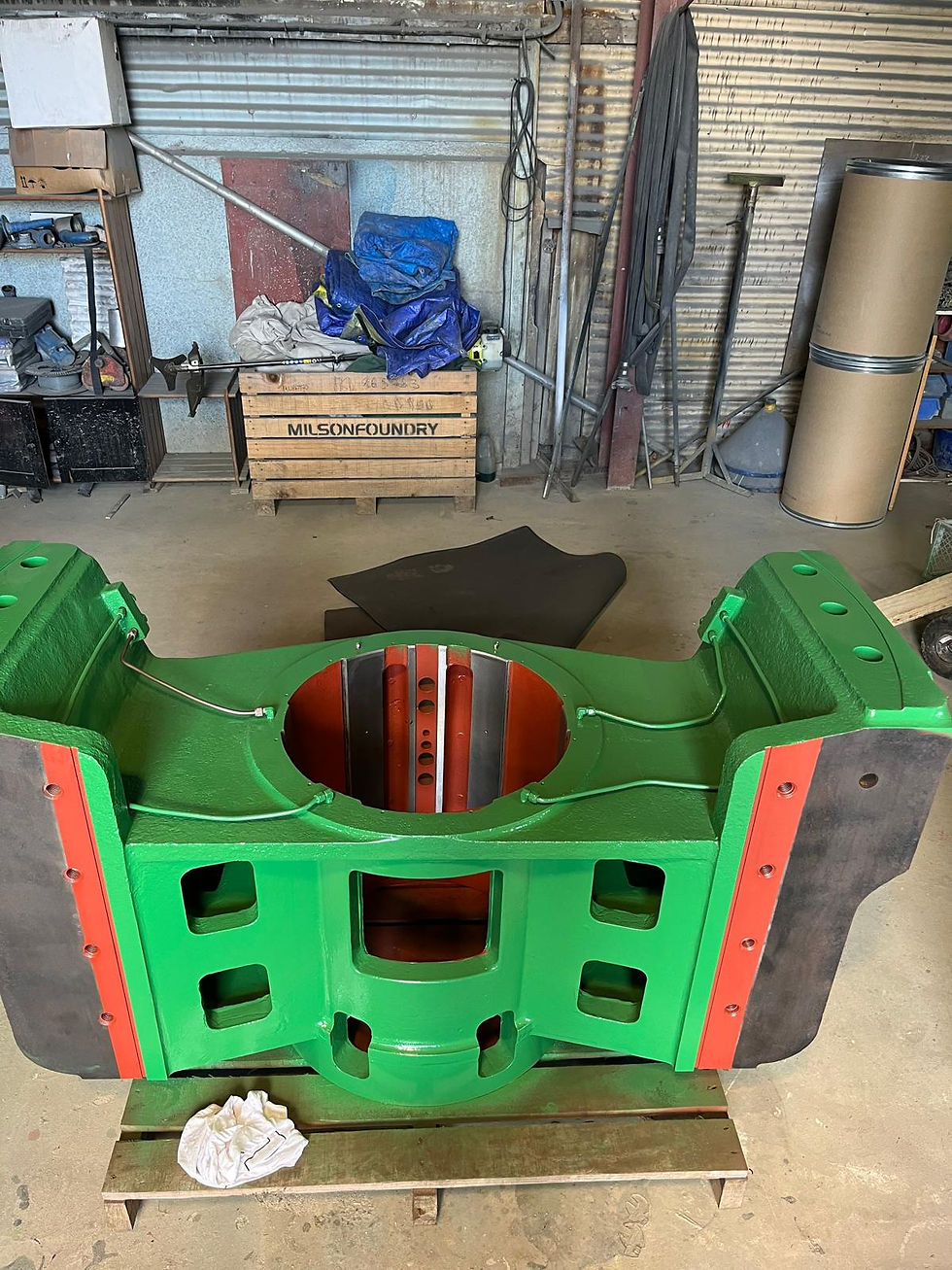
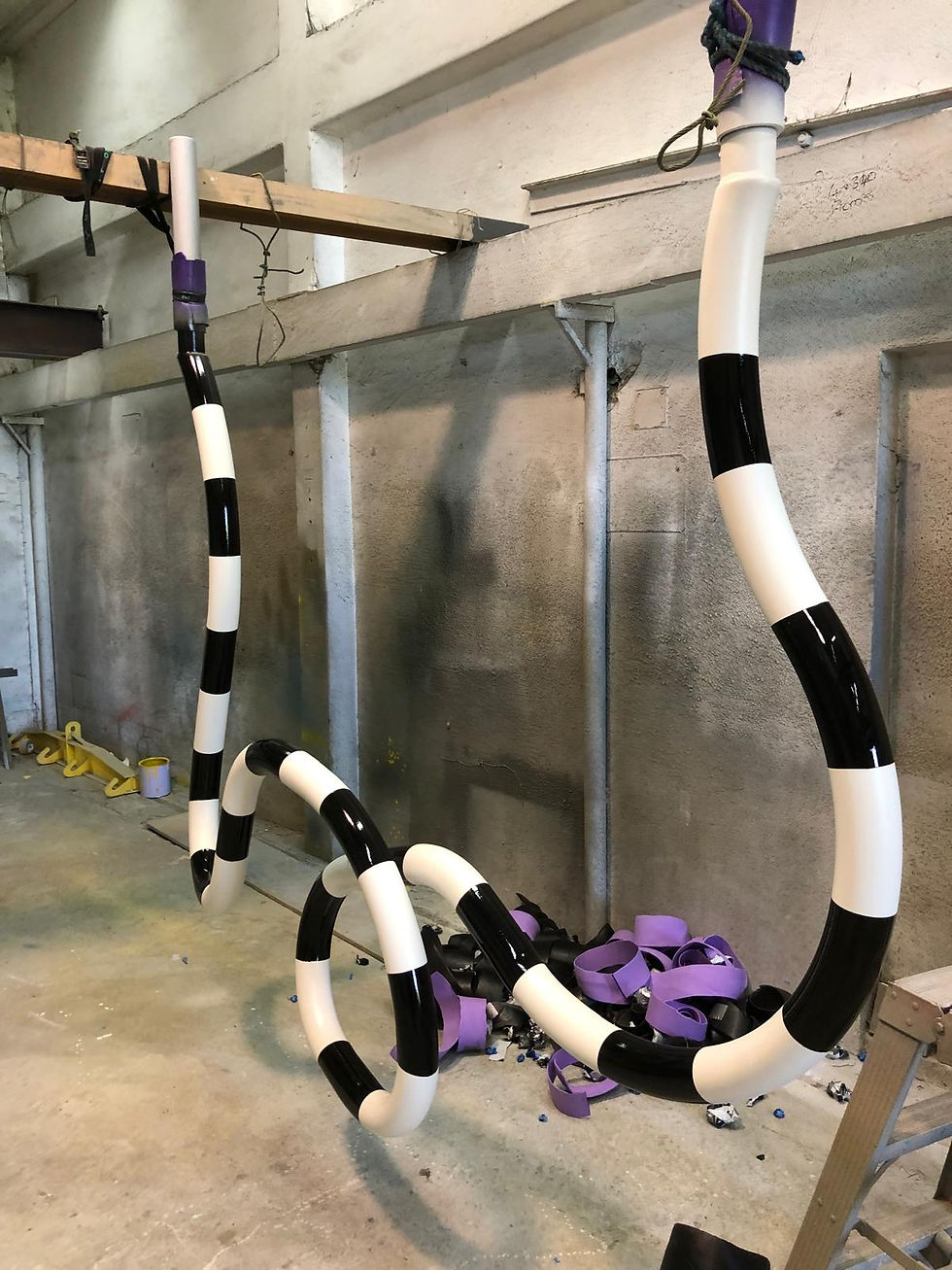
Thermoplastic Flame Spraying Coating
Thermoplastic Flame Spray Coating: Advanced On-Site Corrosion Protection
Triple R Engineering offers Thermoplastic Flame Spray Coating Technology, a cutting-edge solution for applying durable thermoplastic powder coatings directly onto concrete, steel, and other surfaces—without the need for ovens, spray booths, or fluidised bed equipment. This innovative technology enables on-site application, making it an efficient and eco-friendly choice for surface corrosion prevention.
Benefits of Thermoplastic Coating
-
Anti-Osmotic Barrier: Blocks moisture effectively.
-
Superior Adhesion: Ensures lasting performance.
-
Dielectric Insulation: Provides continuous electrical resistance.
-
Abrasion Resistance: Withstands wear and tear.
-
Chemical Resistance: Protects against harsh substances.
-
Flexibility and Repairability: Adapts to repairs and structural movement.
-
Long-Term Protection: Guarantees durability over time.
-
Non-Slip Surface: Enhances safety.
Applications
-
On-Site Coating: Ideal for large, immovable installations like pipes, tanks, and structural components.
-
Restoration & Repair: Revitalize items previously coated using traditional methods like electrostatic or extrusion techniques.
-
Versatile Substrate Compatibility: Applicable to metals, concrete, fiberglass, plastic, wood, and more.
-
Access to Hard-to-Reach Areas: Effective in tight spaces and complex geometries.
-
One-Step Application: Thermoplastic powder is applied directly to pre-treated (abrasive-blasted) and pre-heated surfaces in a single process.
Whether you need industrial-grade protection or repair for challenging surfaces, Thermoplastic Flame Spray Coating is the optimal solution.
Contact Triple R Engineering today to learn how this innovative technology can protect and enhance your assets.

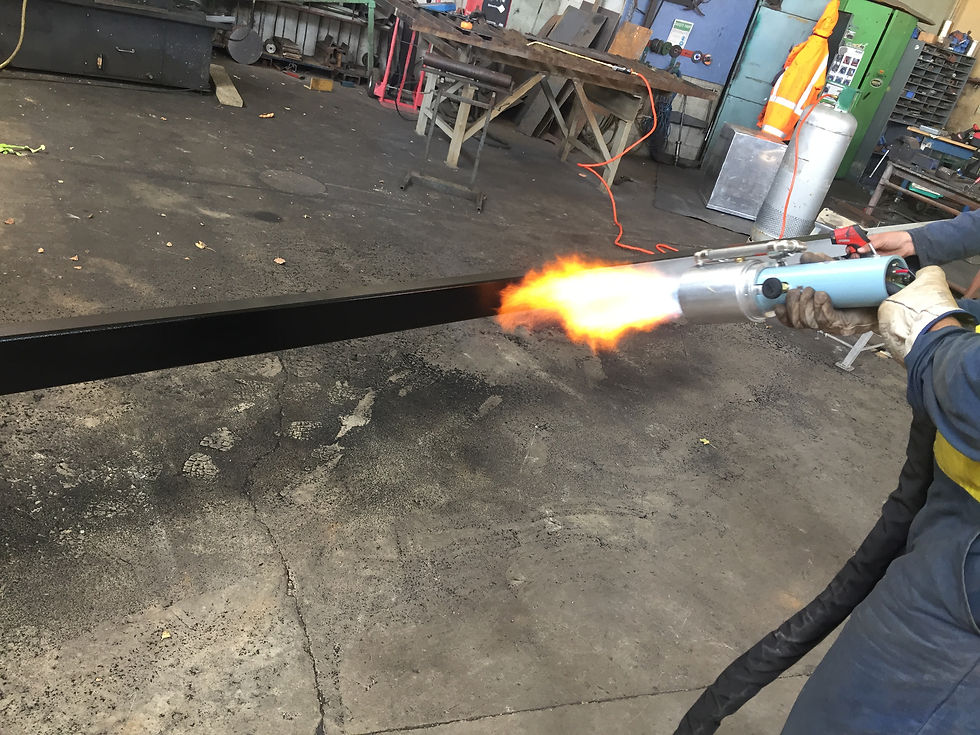
